As unfortunate as it is, musculoskeletal disorders are fairly common in the workplace. Not only are they painful for employees - especially if they are left untreated - they also cost employers billions of dollars in compensation costs and productivity.
In fact, MSDs may be the biggest contributor towards early retirement and disabilities. That said, there are plenty of ways you can prevent MSDs from happening, but you have to be very smart and decisive about when to take action and how.
One such approach to preventing MSDs is to use the hierarchy of controls and implement these to prevent injuries and the risk of MSDs.
Understanding MSDs
Why MSDs are Costly
To understand why control measures are necessary, it's also necessary to understand why MSDs are costly. This is because plenty of the controls used to prevent them can become very costly on their own and many employers may consider not implementing them if only to save the costs for themselves.
This is a bad idea because as mentioned earlier, MSDs on their own can cost employers billions of dollars per year. For example, awkward postures at the workplace cost employers up to $4.71 billion per year, and that is definitely not a small amount. Repetitive motions such as typing can cost employers up to $1.6 billion per year!
In comparison, forking over a few hundred or thousands for the control measures to prevent MSDs is barely anything.
Risk Factors of MSDs
To properly implement the hierarchy of controls, first, it is important to understand the risk factors of MSDs. This is because if you want your implementation to be effective, you also have to consider those risk factors and take steps to make sure each of these is addressed properly.
There are plenty of risk factors that contribute to MSDs. However, from an ergonomic perspective, it is important to keep in mind that MSDs aren't as one-sided as people make them out to be. Some may think MSDs can be attributed entirely to the environment, while others may blame the employee, and others still may blame the work they are doing.
But in reality, it's all of these that play a role!
MSD risks related to the environment revolve around whether the equipment, layout, lighting, etc. are all appropriate for the worker and their work.
On the other hand, MSD risks related to the work may include things like the need to put in excessive force, awkward postures, and tasks that are highly repetitive. High vibrations, impact stress, and other such factors may also play a role.
With regard to workers, MSD risks include things like poor work practices, age, gender, medical history, and all activities they perform outside of work.
MSDs don't develop on their own. They are a result of excessive exposure to some or all of these risk factors and don't develop instantly either. It takes time for the problem to develop and become an MSD. These issues start as fatigue, and will not be as serious.
At this stage, you can recover pretty fast, and may even do so within the day. However, as you keep being exposed to the risk factors, the window you get to recover from the fatigue narrows and there becomes an imbalance.
When this happens, you will find that you are constantly in pain and start seeing some of the early signs of MSDs. This includes things like pain, swelling, loss of motion, numbness, and tingling, among other things. At this stage, however, you are still well within your ability to recover! You'd need to address the issue immediately though, and if you don't, it will eventually develop into an MSD, which is significantly harder to treat and takes much longer.
Hierarchy of Controls
So, now that we know how MSDs work, what causes them, and why they are so important to treat, we can look at the hierarchy of controls you can use to prevent them.
The hierarchy of controls is a framework that is used for getting rid of any hazard - not just ergonomic problems. As a hierarchy, it provides a ranking of all the ways you can control MSDs, from most to least effective.
It goes as follows:
Elimination
Substitution
Engineering Controls
Administrative Controls
PPE
Where elimination is the most effective and PPE is the least effective.
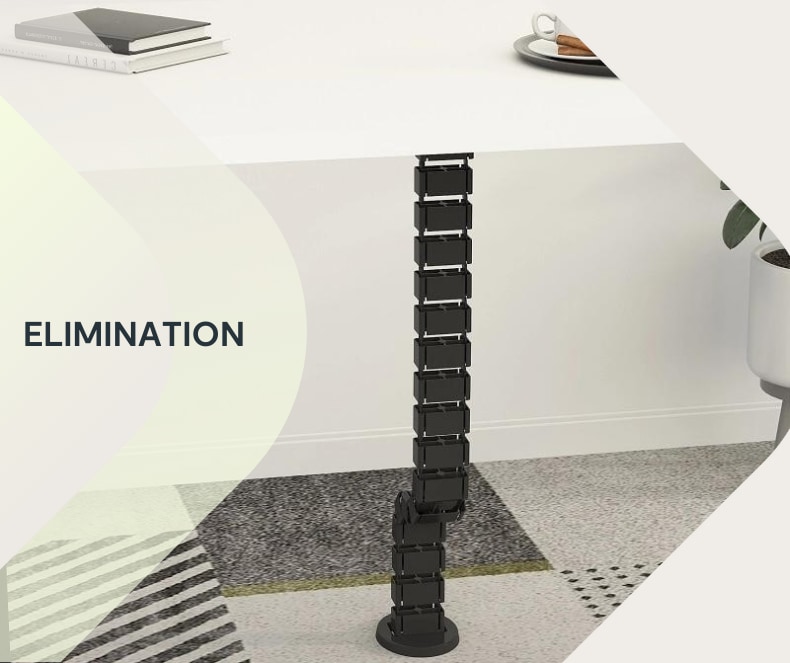
Elimination
Elimination involves removing the hazard entirely. This is understandably the most effective method to prevent MSDs because if the hazard or risk factor doesn't exist at all, there's no way it can contribute to a problem. For example, if there is a risk of tripping and falling due to cables on the ground, you can get use cable management equipment to get rid of the hazard entirely
But elimination is usually very difficult to do for most causes of MSDs and isn't always a viable option.
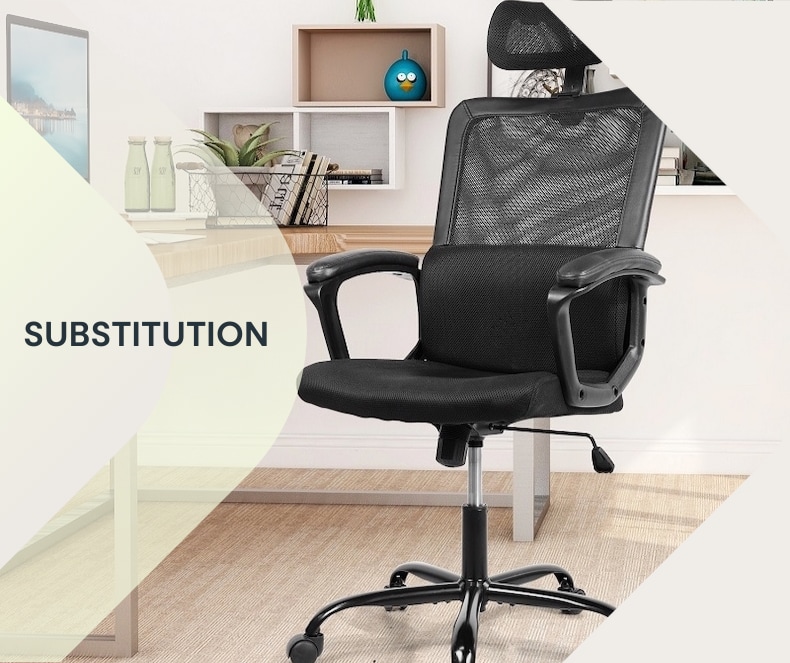
Substitution
Substitution involves replacing the hazard with something else that can get the same task done but without the risk involved - or more commonly, with a lower level of risk than the original hazard. This is easier to do than elimination but is less effective because it doesn't get rid of the risk itself, only reduces it.
For example, you could replace a traditional office chair with an ergonomic one, which can help you prevent problems like lack of lumbar support, and provides armrests, headrests, etc. to support your body. These don't exist in traditional office chairs, so the hazard itself is substituted with something with lower levels of risk.
However, because sitting for long periods of time can still cause MSDs, especially if your work practices aren't keeping ergonomics in mind, you can still be at risk, even with an ergonomic office chair.
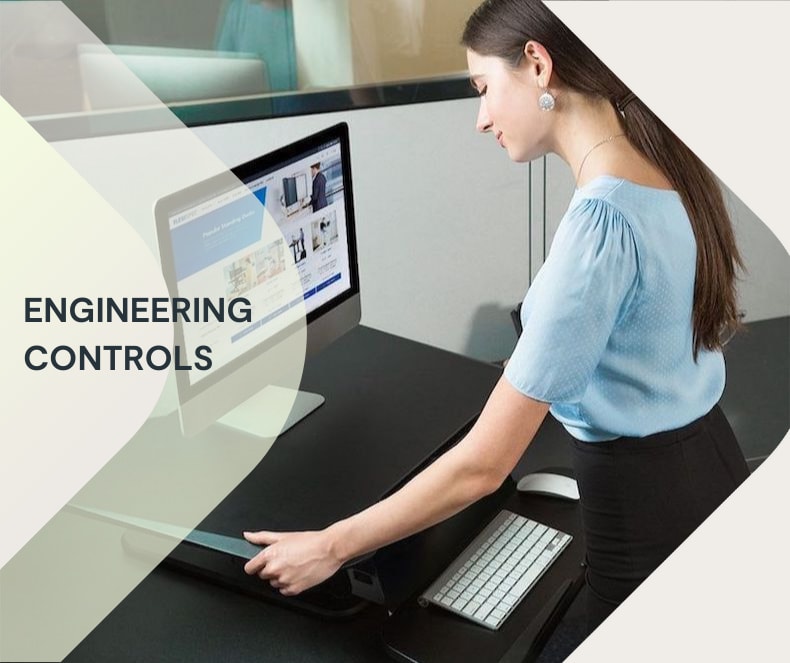
Engineering Controls
Engineering controls refer to modifications to existing equipment or systems which can help reduce the amount of risk posed to workers and keep them safe. For example, you could adjust an existing desk to make it better suited for your height and help you keep proper posture.
This isn't exactly a substitution for the hazard, since the desk remains the same, but there are modifications made to protect the worker from MSDs.
Sometimes, elimination and substitution are also considered part of engineering controls but are usually considered to be separate parts of the hierarchy.
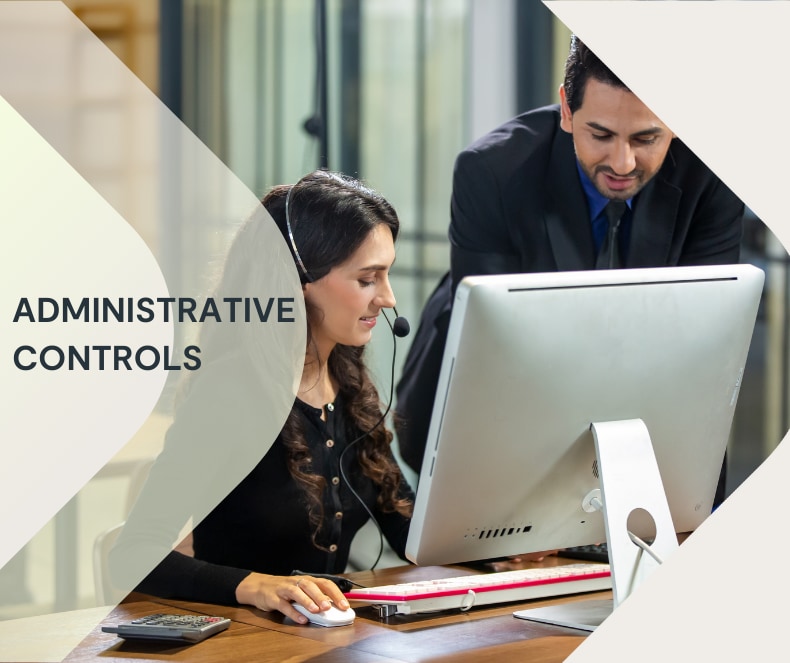
Administrative Controls
Administrative controls refer to making adjustments to processes to protect the worker from injury. In the workplace, this usually involves things like job rotations which help reduce the amount of persistent strain a person is put under, establishing specific work practices that involve more protection, and training to teach individuals how they can work in ways that will protect them.
Administrative controls are trickier than other controls since they involve the need for supervision to make sure that they are being implemented properly and that employees remain safe. However, effective training can be very helpful in making sure that employees do follow the guidelines given to them and protect themselves from risk factors.
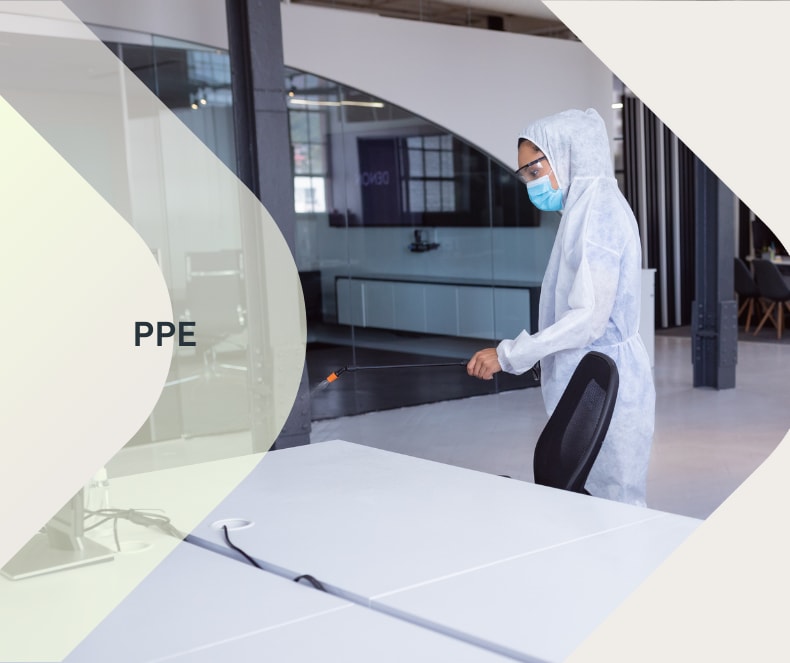
PPE
Personal protective equipment - or PPE - is the last of the controls against hazards, and is also the least effective one. Here, you provide employees with their own protective equipment and expect them to know what to do and how to use them effectively.
This is not as effective because again, it will involve a lot of supervision and you can still never be sure that your employees are using the equipment properly. On top of that, there is always the chance of malfunction, which can result in further injuries and perhaps create even more risks.
However, if you make sure that the PPE is working properly and there are no damages, it is effective at protection and is better than working without any PPE at all.
The important thing to remember about the hierarchy of controls is that you don't have to stick to just one - you can and should be using a mix of them depending on the situation to make sure your employees remain as safe as possible.
The fact is that there isn't going to be only one hazard present at your worksite, and implementing only one control will not be useful when you look at the bigger picture. You have to implement control measures at scale by looking at all the risks present to make sure that injuries don't occur.
It would be best to identify all the risks beforehand so you can prevent injuries, but this is not realistic. Still, it's better late than never, so if a risk becomes apparent to you, address it as soon as possible.